Вопрос 1. Датчики: основные понятия
Первичными преобразователями называют преобразователь, который устанавливают в технологическое оборудование и который первым принимает значение контролируемого параметра, преобразуя его в информацию, передаваемую следующим преобразователям или средствам ее использования.
Информация вырабатывается в таком виде, который не поддается непосредственному восприятию наблюдателя, но является удобной для ее хранения, передачи и преобразования. Первичные преобразователи служат для получения первичной информации о состоянии технологического процесса в системах автоматизации и применяются в автоматизированных системах управления технологическими процессами (Рис.1).
Рис.1. Контроль разрыва ленты емкостным датчиком
Датчиком называют устройство, воспринимающее изменение параметра контролируемой величины и преобразующее это изменение в выходной сигнал. Датчики характеризуются входной и выходной величинами сигнала.
Рис.2. Контроль уровня сыпучих веществ емкостными датчиками
Входная величина – это величина, воспринимаемая и преобразуемая датчиком, например линейное перемещение частей станков, давление в гидро- или пневмосистеме, ток, напряжение, уровень сыпучих веществ (Рис.2 ) и др. параметрические величины.
Выходной сигнал – это определённое качественное или количественное изменение входной величины используемое для передачи на исполнительное или промежуточное звено.
Датчик – устройство, воспринимающее сигналы и внешние воздействия и реагирующее на них, т.е. это преобразователь физической величины (часто неэлектрической) в электрический сигнал. Датчик – измерительное устройство, обеспечивающее преобразование значения физической величины в однозначно соответствующие этому значению характеристики электрического сигнала или информационный сигнал (например: термоэлектронный, давления, расхода).
Общее назначение датчиков – реакция на определенное внешнее физическое воздействие и преобразование его в электрический сигнал, совместимый с измерительными схемами или информационные сигналы. Любой датчик – преобразователь энергии. Вне зависимости от типа измеряемой величины всегда происходит передача энергии от исследуемого объекта к датчику. Работа датчика – это особый случай передачи информации, а любая передача информации связана с передачей энергии.
Преобразователь
– часть датчика, конвертирующая один тип энергии в другой.
Естественный
сигнал - сигнал активного первичного преобразователя или изменение
характеристик измеряемого сигнала в цепи первичного пассивного преобразователя.
Унифицированный
сигнал – пропорциональное значению ФВ значение определенного вида (ток,
напряжение) выходного сигнала преобразователя, в определенным диапазоне его
возможных изменений (например: ток в диапазоне 4-20мА, напряжение в диапазоне
±5В или 0-10В).
- напряжение, ток или заряд,
- значение, амплитуда, частота, фаза или цифровой код.
Каждый датчик характеризуется наборами: входных параметров (любой физической природы) и выходных электрических параметров (Рис.3).
Рис. 3. Индуктивные датчики перемещения и положения для промышленной автоматизации SICK
Чувствительный элемент (для датчика прямого действия) – первичный преобразователь обеспечивающий преобразование внешнего воздействия в электрический сигнал.
- высокая линейность преобразования измеряемой физической величины в максимально широком диапазоне ее изменения,
- воспроизводимость результата в одинаковых условиях измерения,
- высокая стабильность преобразования:
- минимальная зависимость преобразования от значений физической величины и окружающей среды,
- незначительная скорость деградации физических свойств элемента,
- простота конструктивной и технологической защиты элемента от неблагоприятных воздействий измеряемой ФВ и окружающей среды,
- высокая технологичность (дешевизна) изготовления.
В
состав датчика входит один или несколько преобразователей. Например, в
состав химического датчика могут входить два преобразователя, один из которых
конвертирует энергию химических реакций в тепло, а другой, термоэлемент,
преобразовывает полученное тепло в электрический сигнал.
Составной датчик - датчик содержащий несколько преобразователей.
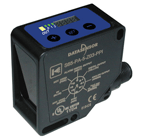
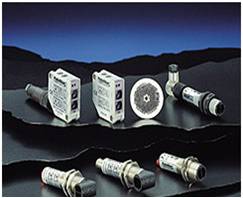
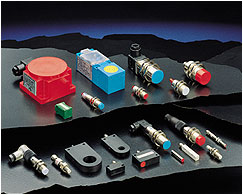
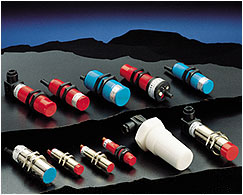
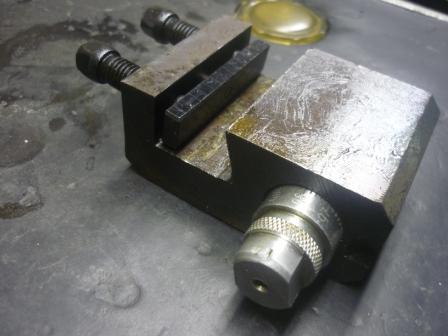
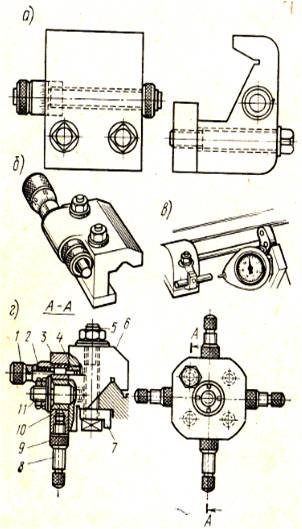
В многопозиционном упоре корпус 6 закрепляют на станине планкой 7 и двумя болтами 5 . В поворотный диск 3 ввернуты четыре установочные винта 8 которые после настройки на длину контрятся гайками 9. В диск 3 запрессована втулка 10, насаживаемая на ось вращения 11. Для смены позиции оттягивают фиксатор Л находящийся под действием пружины 2, и выводят его из втулки 4, запрессованной в корпус 6. После поворота диска на одну полицию фиксатор автоматически заскакивает в следующую втулку 4.
При соприкосновении движущихся частей станка с упором в цепи привода возрастает усилие. Как только оно превзойдет определенную величину, исполнительное звено срабатывает (например, падающий червяк в токарном станке или различные муфты). Иногда упоры воздействуют на систему рычагов (промежуточное звено), а через них на исполнительное звено.
Контакты
изготовляют из материалов, обладающих малыми электрическим сопротивлением,
эрозией и коррозией. Эрозия получается при замыкании и размыкании контакта за
счет дуги, образующейся между ними, и за счет перевеса материала с одного
контакта (анода) на другой (катод) при работе в цепях постоянного тока.
Коррозия - образование значительных оксидных. сульфидных и других пленок на
поверхности контактов, приводящих к разрушению контактной поверхности. Контакты
изготовляют из серебра, меди, золота, вольфрама, молибдена, палладия, никеля,
тантала и др. Вышеуказанные датчики имеют сравнительно большую инерционность,
так как для включения замыкающихся контактов, подающих выходной сигнал,
необходимо переместить контактный мостик на 7—13 мм, на что затрачивается
много времени, а потому такие выключатели применяют при больших скоростях
перемещения (более 0,4 м/мин).
При монтаже датчиков для надежной эксплуатации их необходимо. чтобы усилие, приводящее шток в движение, было направлено вдоль его оси. Допускается использование датчика и при направлении усилия под углом к оси штока. Если упор движется со скоростью до 12 м/мин, то угол должен быть не более 30°, а при скорости кулачка или другого набегающего упора до 60 м/мин угол не более 15°. При медленном движении частей станка (до 0,4 м/мин) и при требованиях повышенной точности изменения положения частей станка, остановки, направления движения и др. (до 0,05 мм) применяют путевые переключатели мгновенного действия (рис. 9,в). При небольших перемещениях частей станка шток датчика должен также иметь очень малое перемещение.
Кроме двухконтактных в некоторых устройствах применяют многопозиционные электроконтактные датчики.
Рис.10. Трёхпозиционный электроконтактный датчик
Шток 1
перемещается в направляющих втулках 8,
расположенных в корпусе 12. На штоке 1 закреплены хомутики 7 и 11,
воздействующие на контактные рычаги 6 и 9, контакты которых могут замыкаться
контактами 2, 3 и 4, регулируемые винтами. Пружина 10 создает определенное
усилие на штоке 1. Рычаг 5 служит арретиром. Датчик имеет четыре положения для
передачи сигнала, когда упор не нажимает
на шток 1, замкнут контакт 2, контакты 3
и 4 разомкнуты; при незначительном перемещении штока 1 под воздействием упора
контакт 2 размыкается, контакты 3 и 4 остаются разомкнутыми; при дальнейшем
перемещении штока 1 под воздействием упора контакт 4 замыкается, а контакты 2 и
3 остаются разомкнутыми; при продолжающемся движении штока 1 под воздействием
упора контакт 2 остается разомкнутым, контакт 3 замыкается.
Многопозиционные датчики сложнее в изготовлении, эксплуатации и значительно дороже двухконтактных. Путевые электроконтактные датчики имеют пределы измерения 0—25 мм с предельной погрешностью до ±0,5 мкм.
Индуктивные путевые датчики. При большой частоте включений и выключений электроконтактные датчики быстро теряют точность и выходят из строя, поэтому их заменяют бесконтактными, в частности индуктивными, которые значительно увеличивают точность измерения.
Индуктивные датчики широко применяют в копировальных устройствах металлорежущих станков, а также для точных измерений величин в системах автоматического контроля и отсчета. Пределы измерений индуктивных датчиков 0-0,8 мм при предельной погрешности измерений до -0,3 *мкм.
Они
работают на токе промышленной частоты, длительно эксплуатируются и дешевы в
изготовлении.
Рис.11. Индуктивный датчик
Индуктивный датчик (рис. 11, а) имеет две катушки 1 и 3 с обмотками. Между катушками расположен якорь 2, находящийся под воздействием штока 4. Первичные обмотки катушек включены последовательно и питаются переменным током. Вторичные обмотки включены встречно, поэтому, когда якорь находится в среднем положении, напряжение на выходе датчика равно нулю. При перемещении якоря (рис. 11, б) воздушный зазор 6 у одной катушки увеличивается, у другой уменьшается. При этом изменяются магнитные потоки Ф и с ними индуктивные сопротивления и токи в катушках. Катушки z1 и z2 включенные в мостовую схему (рис. 11, в) V. являются ее плечами, а катушки z1 и z2 выполняют компенсационную роль. При смещении якоря от середины нарушается симметричность плеч моста — в систему поступает электрический сигнал, величина которого указывается измерительным прибором И, включенным в схему. При изменении зазора изменяется и его сопротивление, а следовательно, и индуктивность катушки и ток.
Повысить чувствительность индуктивных датчиков можно при уменьшении магнитного сопротивления в воздушном зазоре. Для этого увеличивают количество рабочих граней, т. е. создают полюсные наконечники на сердечниках и якоре не плоской, а зубчатой формы. Одновременная работа нескольких зубцов повышает чувствительность датчика. Так, например, сердечники 1 и 3 (рис. 11, а) установлены так, что их зубцы сдвинуты на толщину зубца якоря 2. При перемещении зубцы якоря, приближаясь к зубцам одного сердечника, удаляются от зубцов другого. Равновесие электросхемы в плечах моста, куда включены обмотки z1 и z2 нарушается. Когда величина зазора Ь между гранями зубцов якоря в обоих сердечниках будет одинакова, наступает равновесие (нулевое значение тока), которое при перемещении якоря вдоль сердечников будет повторяться через каждый шаг Т определяемый размером зубца и впадины.
В
остальных положениях якоря величина тока будет изменяться соответственно
степени разбаланса датчика. Максимальное значение тока соответствует
максимальной величине разбаланса. Это позволяет подсчитать количество
пройденных шагов, используя импульсы тока, а также установить якорь в нулевое
положение с высокой точностью.
Гидравлические и пневматические путевые датчики. В гидравлических системах изменением величины и направления потока рабочей жидкости (масла) к исполнительному звену регулируют работу механизмов. Датчиками гидравлических систем служат золотники.
Рис.12. Гидравлический датчик-золотник
Гидравлический датчик золотник (рис. 12) позволяет изменять направление жидкости, поступающей в | одну или другую полость исполнительного звена (силового цилиндра), либо от одного исполнительного звена к другому. Когда движущаяся часть станка нажмет на рычаг 10, он поворачивается вокруг оси 1 и тянет влево плунжер 6. При этом жидкость, нагнетаемая в трубопровод 7 и ранее подававшаяся через камеру в канал 3, изменит направление и начнет поступать в канал 4, так как канал 3 перекроется плунжером. Чтобы при перекрытии каналов избежать больших гидравлических ударов, в золотнике предусмотрено устройство, замедляющее ход плунжера. Это устройство состоит из камеры с полостью а, трубопровода 2 и дросселя 5, заполненных маслом. Резкому движению плунжера препятствует масло, перекачиваемое из полости а в полость б плунжером при движении влево, из полости, б в полость а, при движении плунжера вправо. Сопротивление движению плунжера регулируется дросселем 5. На рычагах 10 и 9 имеются скосы, чтобы при повороте рычага 10 рычаг 9 легче отжимался вниз, а затем под действием пружины 8 вновь поднимался вверх, фиксируя рычаг 10 в повернутом положенииПневматические путевые датчики изменяют направление потока воздуха, чтобы закрыть или открыть доступ воздуху к исполнительному звену. Такие датчики, аналогично гидравлическим, выполняют в виде золотников, кранов и клапанов.Рис.13. Пневматический датчик
Многие пневматические датчики полностью срабатывают лишь при значительных перемещениях частей станка (10—13 мм). На рис. 13 приведена конструкция датчика, срабатывающего при перемещении на 1—1,5 мм. Движущаяся часть станка перемещает шток 6 вправо или влево. В положении, показанном на рисунке, воздух из магистрали через каналы 1, 3, 4 поступает к исполнительному звену. Каналы 11, 9, 8, сообщающиеся с атмосферой, перекрыты шариковым клапаном 10. При перемещении штока 6 влево плунжер 5 и шариковый клапан 2 под действием пружины опускаются вниз, а плунжер 7 и клапан 10, сжимая пружину, поднимается вверх. При этом перекрывается канал 3 и прекращается подача воздуха из магистрали, а через каналы 4, 11, 9, 8 воздух выходит в атмосферу.