Тема 1.3. Системы автоматического управления
Вопросы:
1. Автоматизированная система управления (АСУ): принципы построения АСУ, состав и технические средства.
2. Функциональная схема САУ
замкнутой и разомкнутой.
3. Законы автоматического управления.
4. Исполнительные элементы САУ.
5. Статические и астатические системы
6. Система автоматизированного управления производством.
Вопрос 1. Автоматизированная система управления (АСУ)
Системы управления работой автоматических пли полуавтоматических машин (металлорежущих станков) являются комплексом механизмов и устройств, служащим для сообщения рабочим органам (РО) станка действий, необходимых при обработке детали на станке без участия человека.
Автоматизированная система управления (АСУ) –это система, призванная обеспечивать автоматизированный сбор и обработку информации, необходимый для оптимизации процесса управления.
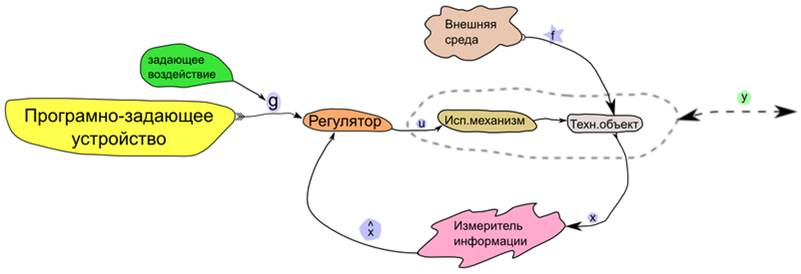
Рис. 1
По виду задающей информации системы управления делятся на системы с нечисловых (путевые, кулачковые и копировальные], с частично числовым (цикловые программные), с чистовым программным управлением (ЧПУ) и комбинированные. Задающая информация в системах с нечисловым управлением дается в виде физического аналога, в системах с ЧПУ — в виде комбинации чисел, в цикловых — частично аналогом, частично в виде чисел.
Путевые системы управления наиболее просты из всех указанных, но обеспечивают наименьшую автоматизацию управления. Они управляют скоростью движения, поэтому в случае их применения нет информации об изменении скорости движения, информация о пройденном нуги задается требуемой установкой упоров, а информация о цикле обеспечивается непереналажнваемой релейной схемой автоматики. В кулачковых и копировальных системах управления информация (о пути, скорости и цикле) задается соответственно кулачками распределительного механизма и копирами или шаблонами.
Принципы построения АСУ
- Системность;
- Развитие (открытость);
- Совместимость;
- Стандартизация (унификация);
- Эффективность;
- Надежность.
Технические средства АСУ
Кулачковые системы управления
Кулачковые механизмы широко применяются в станках-автоматах и других машинах для осуществления автоматического цикла работы. Эти механизмы могут быть с дисковым цилиндрическим и плоским кулачками (Рис.2). Дисковые кулачки с силовой связью применяют в небольших станках с малой массой суппорта во избежание сильных ударов, происходящих при отводе рабочего органа. Угол подъема профиля кулачка с кинематической связью на участках быстрого перемещения рабочего органа из-за возможного заклинивания толкателя следует выбирать в пределах 45-55°.
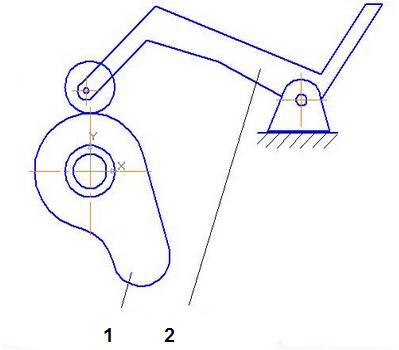
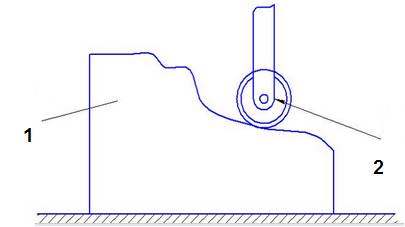
Рис. 2. Кулачковая система управления с дисковым и плоским кулачком: 1-кулачок; 2-толкатель
Кулачки передают поступательное или качательное движение толкателям. Профиль кулачков состоит из цилиндрической поверхности, подъемов и спусков. При соприкосновении с цилиндрическим участком рычаг-толкатель (балансир) не отклоняется от своей оси, и поэтому суппорт или другой рабочий орган не изменяет своего положения. На участках подъема и спуска рычаг отклоняется от предшествующего положения относительно оси и передает соответствующее движение рабочему органу. Профиль кулачков соответствует требуемой программе движения исполнительных звеньев. Кулачковые системы с распределительным валом являются очень надежными механическими системами с контурным управлением (со сложным формообразованием); станки имеют жесткую конструкцию и обеспечивают высокую точность повторения размеров. Они стабильно поддерживают постоянную во времени синхронизацию цикла. Система управления широко распространена и сохранится в дальнейшем в автоматах для массового и крупносерийного производства относительно небольших изделий типа тел вращения с устойчивой номенклатурой (так как время переналадки кулачковых автоматов значительно).
Копировальные системы управления
Другой системой контурного управления механического типа является копировальная система, в которой копир можно рассматривать как кулачок, развернутый на плоскость. Вместо распределительного вала применен крестовый суппорт, обеспечивающий синхронизацию ведущего движения Sg от гидроцилиндра / (при продольном движении каретки-2) со следящим движением S щупа 3, получаемым от копира 4 (движение поперечной каретки 5). Резец 6 совершает одновременное (суммарное) движение в продольном и поперечном направлениях. В этой системе программоносителем является профиль копира, а траектории простых движений определяются направляюшцми суппорта (внутренним источником информации станка). В копировальных системах управления отсутствует активный поток информации о фактическом положении исполнительного устройства, поэтому их относят к системам управления незамкнутого типа.
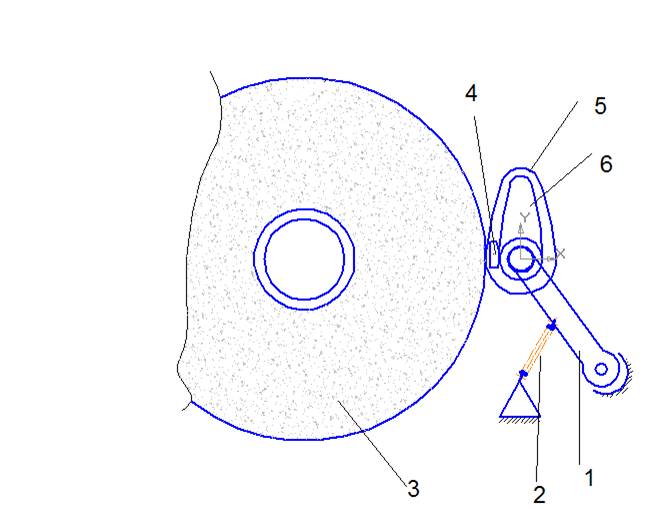
Рис. 3 Копировальные системы управления
- Рычаг
- Пружина
- Круг
- Упор
- Деталь
- Копир
Системы управления с командоаппаратом.
- Рис. 4. Системы управления с командоаппаратом
- Ролик
- Защелка
- Кулачок
- Диск
- Кулачок
- Рычаг
Числовые программные системы управления. В стайках с ЧПУ информация, необходимая для выполнения
запроектированной механической обработки детали, задается в числовом виде и
записывается в условном коде на программоносителе. Программоноситель с
необходимой информацией обработки детали вводится в специальное считывающее
устройство станка. При перемещении программоносителя в считывающем устройстве
из него в соответствующее устройство системы поступает числовая информация,
которая преобразуется в электрические импульсы, используемые для заданных
перемещений рабочих органов станка.
При обработке деталей на
станках с числовым программным управлением работа наладчика заключается в
установке, закреплении и снятии детали, смене затупившегося режущего
инструмента, периодическом контроле деталей и наблюдении за работой станка.
Точность размеров, форма и шероховатость поверхностей обрабатываемой детали и
время, затрачиваемое на ее обработку, зависят от правильности расчетов
программы работы станка. В станках с ЧПУ нет физического носителя
выдерживаемых размеров обрабатываемых деталей, а программа, управляющая
рабочими органами станка, записывается в математической форме в виде чисел на
программоноситель.
Принципиальная особенность
станка с ЧПУ — это работа по управляющей программе (УП), на которой записаны
цикл работы оборудования для обработки конкретной детали и технологические
режимы. При изменении обрабатываемой на станке детали необходимо просто сменить
программу, что сокращает на 80...90 % трудоемкость переналадки по сравнению с
трудоемкостью этой операции на станках с ручным управлением. При изготовлении
деталей со сложными пространственными профилями в единичном и мелкосерийном
производстве использование станков с ЧПУ является почти единственным технически
оправданным решением. Это оборудование целесообразно применять и в случае, если
невозможно быстро изготовить оснастку. В серийном производстве также
целесообразно использовать станки с ЧПУ. В последнее время широко используют
автономные станки с ЧПУ или системы из таких станков в условиях
переналаживаемого крупносерийного производства.
Основные преимущества станков с ЧПУ:
- производительность станка повышается в 1,5... 2,5 раза по сравнению с производительностью аналогичных станков с ручным управлением;
- сочетается гибкость универсального оборудования с точностью и производительностью станка-автомата;
- снижается потребность в квалифицированных рабочих-станочниках, а подготовка производства переносится в сферу инженерного труда;
- детали, изготовленные по одной программе, являются взаимозаменяемыми, что сокращает время пригоночных работ в процессе сборки;
- сокращаются сроки подготовки и перехода на изготовление новых деталей благодаря предварительной подготовке программ, более простой и универсальной технологической оснастке;
- снижается продолжительность цикла изготовления деталей и уменьшается запас незавершенного производства.
- производительность станка повышается в 1,5... 2,5 раза по сравнению с производительностью аналогичных станков с ручным управлением;
- сочетается гибкость универсального оборудования с точностью и производительностью станка-автомата;
- снижается потребность в квалифицированных рабочих-станочниках, а подготовка производства переносится в сферу инженерного труда;
- детали, изготовленные по одной программе, являются взаимозаменяемыми, что сокращает время пригоночных работ в процессе сборки;
- сокращаются сроки подготовки и перехода на изготовление новых деталей благодаря предварительной подготовке программ, более простой и универсальной технологической оснастке;
- снижается продолжительность цикла изготовления деталей и уменьшается запас незавершенного производства.
Системы программного управления металлорежущими станками по конструктивному признаку разделяются на системы с числовым программным управлением (СЧПУ) и системы с программированием цикла и режимов обработки.
В моделях станков
с ПУ для обозначения степени автоматизации добавляется буква Ф с цифрой:
Ф1 —
станки с цифровой индикацией и преднабором координат;
Ф2 — станки с
позиционными и прямоугольными системами ЧПУ;
ФЗ — станки с контурными системами
ЧПУ и Ф4 — станки с универсальной системой ЧПУ для позиционной и контурной
обработки.
Особую группу составляют станки, имеющие ЧПУ для многоконтурной
обработки, например бесцентровые круглошлифовальные станки. Для станков с
цикловыми системами ПУ в обозначении модели введен индекс Ц, с оперативными
системами — индекс Т (например, 16К20Т1).
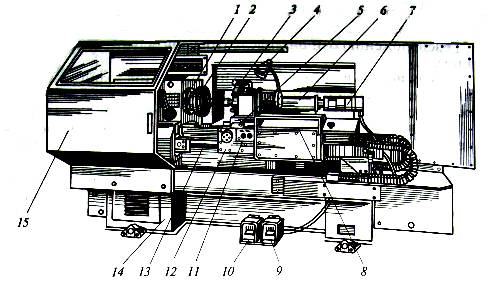
Рис.5. Токарный патронно-центровой станок с оперативной системой ЧПУ: 1-шпиндельная бабка; 2-патрон; 3-револьверная головка; 4-лампа местного освещения; 5-суппорт; 6-задняя бабка; 7-электродвигатель; 8-панель управления УЧПУ; 9-педаль отжима пиноли задней бабки; 10-педаль включающая перемещение пиноли задней бабки к шпинделю; 11-кнопочная станция включения (выключения) привода главного движения; 12-фартук; 13-ходовой винт; 14-станина; 15-защитный кожух
Для станков с ЧПУ
стандартизованы направления перемещений и их символика. Стандартом ISO-R841
принято за положительное направление перемещения элемента станка считать то,
при котором инструмент или заготовка отходят один от другого. Исходной осью (ось
Z) является ось рабочего шпинделя. Если эта ось поворотная, то ее положение
выбирают перпендикулярно плоскости крепления детали. Положительное направление
оси Z— от устройства крепления детали к инструменту. Тогда оси Х и Y
расположатся так, как это показано на рис. 5.
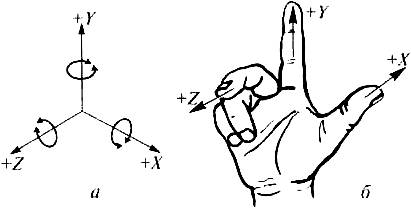
Рис. 5.
Расположение осей координат в станках с ЧПУ (а); правосторонняя система
координат (б)
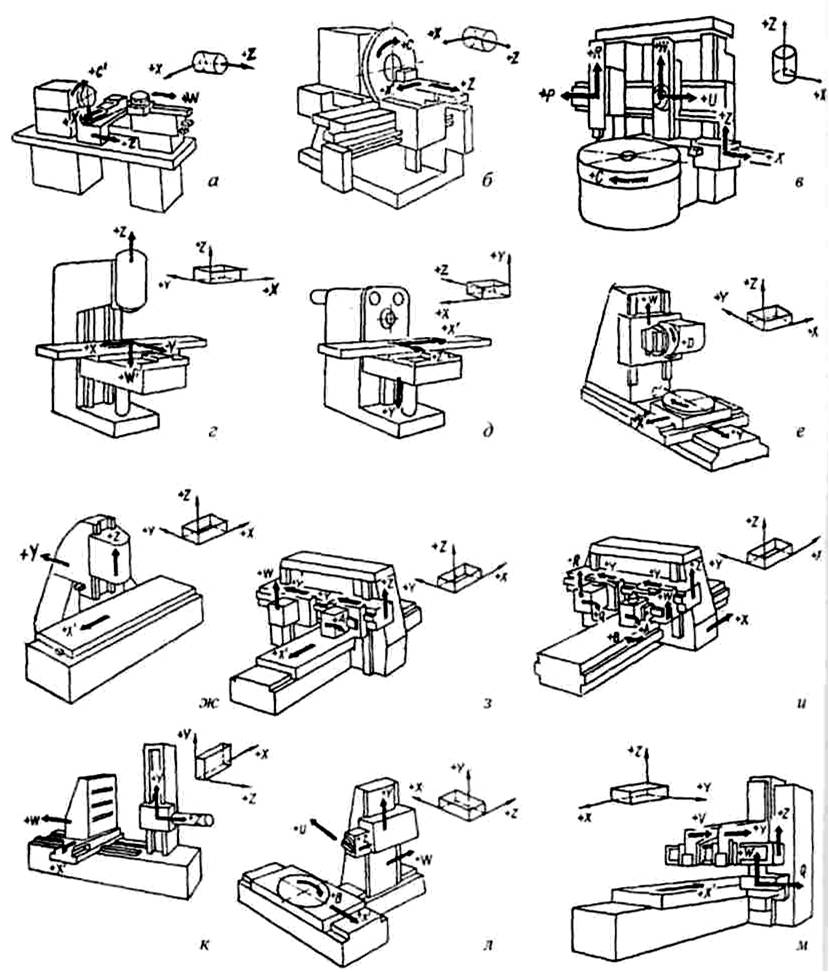
Рис. 6 –
Обозначение осей координат и направлений перемещений на схемах станков с ЧПУ:
а – токарно-револьверного; б – лоботокарного; в-токарно-карусельного;
г – вертикально-фрезерного; д – горизонтального консольно-фрезерного;
е – фрезерного с поворотным столом и поворотной бабкой; ж – вертикального портально-фрезерного; з – двухстоечного портально-фрезерного; и – двухстоечного с подвижным порталом; к – горизонтально-расточного с неподвижной передней бабкой; л- с продольно-подвижной передней бабкой; м – продольно-строгального
а – токарно-револьверного; б – лоботокарного; в-токарно-карусельного;
г – вертикально-фрезерного; д – горизонтального консольно-фрезерного;
е – фрезерного с поворотным столом и поворотной бабкой; ж – вертикального портально-фрезерного; з – двухстоечного портально-фрезерного; и – двухстоечного с подвижным порталом; к – горизонтально-расточного с неподвижной передней бабкой; л- с продольно-подвижной передней бабкой; м – продольно-строгального
Вопрос 2. Функциональная схема САУ замкнутой и разомкнутой
Вопрос 3. Законы автоматического управления
Вопрос 4. Исполнительные элементы САУВопрос
5. Статические и астатические системы
Статической характеристикой звена или системы - называют зависимость выходной величины от различных постоянных значений входной величины в установившихся режимах.
Статическая характеристика:
- По каналу задающего воздействия
- По каналу возмущающего воздействия
Статической системой принято считать :
- (относительно задающего воздействия) , если при любом постоянном задающем воздействии установившаяся ошибка регулирования достаточно мала, но не равна нулю;
- (относительно возмущающего воздействия), если при различных постоянных значениях возмущающего воздействия регулируемая величина изменяет свое значение пропорционально возмущающему воздействию.
Астатической системой принято считать :
- (относительно задающего воздействия), если при любом постоянном задающем воздействии установившаяся ошибка регулирования равна нулю;
- (относительно возмущающего воздействия), если при различных постоянных значениях возмущающего воздействия по окончании переходного процесса отклонение регулируемой величины от заданного значения равно нулю
Вопрос 6. Система автоматизированного управления производством
Управление – это процесс достижения человеком или группой лиц цели управления при наличии определенной информации.
Акт целенаправленного воздействия на управляемый процесс, основанный на информации о нем, определенной ранее цели разработанной программе достижения этой цели, называется принятием решения.
Информационные технологии управления в промышленных комплексах, несмотря на затянувшийся экономический спад, нехватку средств у предприятий, современные компьютерные технологии постепенно становятся повседневным инструментом руководителей.
Для успешного функционирования промышленных предприятий в современных условиях важнейшую роль играют информационные технологии, позволяющие не только решать широкий круг задач в сфере автоматизации финансово-хозяйственной и управленческой деятельности. Основной способ совершенствования работы предприятий в настоящее время: внедрение современных компьютерных технологий управления
При наличии локальных вычислительных сетей на предприятии, можно выделить следующие положительные факторы:
- организуется автоматизированный документооборот
- создаются различные массивы управленческой, коммерческой информации общего назначения
- появляются возможности использования различных средств решения определенных профессиональных задач(например: средств машинной графики, подготовки отчетов, ведомостей, докладов и других документов).
Входящие - документы, поступившие из внешней среды, регламентирующие деятельность, поступающие из Министерства Транспорта, налоговых органов, органов санэпиднадзора.Большинство входящих документов порождают соответствующие исходящие, причем в четко установленные сроки. Сроки устанавливаются либо нормативными актами, предписывающими то или иное время ответа на документ, или сроком исполнения, указанным непосредственно во входящем документе.
2. Исходящие. Большинство исходящих документов являются ответом предприятия на соответствующие входящие документы. Это отчеты, справки, предоставляемые в вышестоящие и контролирующие органы, документы бухгалтерской отчетности. Все они сопровождаются сопроводительными письмами.
3. Внутренние. Данные документы используются для организации работы предприятия.
Существует два подхода к выбору программных средств:
- Создание программного продукта с требуемым набором функций средствами предприятия(написание программ штатными программистами)
- Использование стандартного программного обеспечения
ETHERNET
На
уровне управления производством сети Ethernet уже давно завоевали себе прочное лидирующее место.
Решения на базе Ethernet практически вытеснили все остальные из офисных распределенных приложений, и сегодня Ethernet является основным средством обмена в локальных сетях. В
последнее время Ethernet стал активно
проникать и в комплексы управления производственными процессами. Появился целый ряд аппаратных средств (коммутаторов
и концентраторов), выполненных в
соответствии с требованиями промышленных условий эксплуатации.
Использование Ethernet, как физической среды передачи данных, приводит к использованию хорошо адресуемых логических протоколов. Уже сейчас большинство устройств поддерживают протокол TCP/IP. Это позволяет легко интегрировать локальные системы управления технологическими процессами в сети любого масштаба, включая глобальную сеть Internet.
Отличительные особенности сети Industrial Ethernet:
– Промышленная сеть верхних уровней управления, отвечающая требованиям международного стандарта IEEE 802.3 (Ethernet);
– Обеспечение гомогенной и гетерогенной связи между системами автоматизации, компьютерами и рабочими станциями;
– Возможность применения открытых сетевых решений;
– Общепризнанный мировой стандарт организации промышленной связи.
– Основа для применения информационных технологий в системах автоматизации
– Поддержка Web функций, функций электронной почты, WAN связи;
– Простое и быстрое подключение сетевых компонентов;
– Высокая гибкость: существующие сети могут расширяться без их остановки;
– Высокая надежность, достигаемая использованием резервированных топологий;
– Возможность применения в офисных и промышленных условиях;
– Использование оборудования множества производителей за счет подключения к WAN (wide area network), например, ISDN или Internet;
– Высокая производительность. Так выпускавшиеся ранее компоненты SIMATIC NET для Industrial Ethernet со скоростью передачи данных 10Мбит/с дополнены новыми компонентами Fast Ethernet со скоростью передачи данных 100Мбит/с.
Сеть Fast Ethernet является дальнейшим развитием технологии Ethernet. Стандарт Fast Ethernet IEEE 802.3u в основном базируется на классическом стандарте Ethernet для промышленных витых пар и предусматривает увеличение скорости передачи данных с 10 до 100Мбит/с. Новый стандарт позволяет получить целый ряд преимуществ:
– В сетях Fast Ethernet могут использоваться все существующие наработки для Ethernet, причем, дополнительных знаний не требуется;
– Технология Fast Ethernet может вводиться в действие на объектах Ethernet немедленно;
– Industrial Ethernet поддерживает поэтапный переход от 10 к 100Мбит/с технологии
Использование Ethernet, как физической среды передачи данных, приводит к использованию хорошо адресуемых логических протоколов. Уже сейчас большинство устройств поддерживают протокол TCP/IP. Это позволяет легко интегрировать локальные системы управления технологическими процессами в сети любого масштаба, включая глобальную сеть Internet.
Отличительные особенности сети Industrial Ethernet:
– Промышленная сеть верхних уровней управления, отвечающая требованиям международного стандарта IEEE 802.3 (Ethernet);
– Обеспечение гомогенной и гетерогенной связи между системами автоматизации, компьютерами и рабочими станциями;
– Возможность применения открытых сетевых решений;
– Общепризнанный мировой стандарт организации промышленной связи.
– Основа для применения информационных технологий в системах автоматизации
– Поддержка Web функций, функций электронной почты, WAN связи;
– Простое и быстрое подключение сетевых компонентов;
– Высокая гибкость: существующие сети могут расширяться без их остановки;
– Высокая надежность, достигаемая использованием резервированных топологий;
– Возможность применения в офисных и промышленных условиях;
– Использование оборудования множества производителей за счет подключения к WAN (wide area network), например, ISDN или Internet;
– Высокая производительность. Так выпускавшиеся ранее компоненты SIMATIC NET для Industrial Ethernet со скоростью передачи данных 10Мбит/с дополнены новыми компонентами Fast Ethernet со скоростью передачи данных 100Мбит/с.
Сеть Fast Ethernet является дальнейшим развитием технологии Ethernet. Стандарт Fast Ethernet IEEE 802.3u в основном базируется на классическом стандарте Ethernet для промышленных витых пар и предусматривает увеличение скорости передачи данных с 10 до 100Мбит/с. Новый стандарт позволяет получить целый ряд преимуществ:
– В сетях Fast Ethernet могут использоваться все существующие наработки для Ethernet, причем, дополнительных знаний не требуется;
– Технология Fast Ethernet может вводиться в действие на объектах Ethernet немедленно;
– Industrial Ethernet поддерживает поэтапный переход от 10 к 100Мбит/с технологии
HART –
протокол
Унифицированный сигнал 4-20
мА для передачи аналоговых сигналов
известен несколько десятков лет и широко используется при создании АСУ ТП в различных отраслях
промышленности. Достоинством
данного стандарта является простота его реализации, использование его во
множестве приборов, возможность помехоустойчивой передачи аналогового сигнала
на относительно большие расстояния. Однако при создании нового поколения
интеллектуальных приборов и датчиков
потребовалось наряду с аналоговой информацией передавать и цифровые данные, соответствующие их новым
расширенным возможностям.
С этой
целью американской компанией Rosemount был разработан протокол HART (Highway Addressable Remote Transducer). HART-протокол основан на
методе передачи данных с помощью частотной модуляции, при этом цифровой сигнал
накладывается на аналоговый токовый сигнал.
Частотно-модулированный
сигнал является двухполярным и при использовании соответствующей фильтрации не
искажает основной аналоговый сигнал 4-20 мА. Основные технические параметры,
определяемые
стандартом на HART-протокол:
– Топология «Точка-точка» (стандартная) или шина;
– Максимальное количество устройств -
одно
ведомое и два
ведущих устройства (стандартный режим), 15 ведомых и 2
ведущих устройств (многоточечный режим с
удаленным питанием);
– Максимальная
протяженность линии связи - 3 км (стандартный режим), 100
м
(многоточечный режим);
– Тип линии – экранированная витая пара;
– Интерфейс – 4-20 мА, токовая петля (аналоговый);
– Время цикла обновления данных
- около 500 мс.
HART-протокол может
использоваться в двух режимах работы:
1. Стандартный вариант - соединение
«точка-точка», т.е. непосредственное соединение прибора низовой автоматики
(датчика, исполнительного
механизма, преобразователя) и не более двух ведущих устройств. В качестве первичного
ведущего устройства используется
устройство связи с
объектом (УСО) или
программируемый логический контроллер (ПЛК). В качестве вторичного
применяется портативный HART-терминал или персональный
компьютер с HART-модемом. При этом
аналоговый сигнал является однонаправленным (например, от датчика к ПЛК или от ПЛК к
исполнительному механизму), а цифровые сигналы могут передаваться и приниматься
как от ведущего, так и от ведомого устройства.
2. Многоточечный режим - 15 ведомых
устройств могут соединяться параллельно двухпроводной линией с теми же двумя ведущими устройствами.
При этом осуществляется только цифровая связь. Сигнал постоянного тока 4 мА
обеспечивает вспомогательное питание ведомых приборов по сигнальным линиям.
CAN – протокол
Протокол
CAN (Controller Area Network) был предложен
компанией Bosch для создания сети
контроллеров в автомобилях. В настоящее время CAN-сети
активно применяются в самых разных областях (от стиральных машин до
космических аппаратов). Протокол CAN определяет только первые два уровня модели
ISO/OSI - физический и канальный. На основе этого
протокола реализовано огромное количество
полнофункциональных сетей, таких как CANOpen, DeviceNet, SDS и др. Количество узлов промышленных сетей, работающих на основе CAN, исчисляется десятками миллионов. Практически у каждого
крупного
производителя микроконтроллеров есть изделие с CAN-интерфейсом. Широкому распространению CAN способствуют его многочисленные
достоинства, среди которых:
– Невысокая
стоимость, как самой сети, так и ее разработки;
– Высокая степень надежности
и живучести сети, благодаря развитым
механизмам обнаружения ошибок, повтору ошибочных сообщений,
самоизоляции неисправных узлов, нечувствительности к электромагнитным помехам;
– Простота конфигурирования и
масштабирования сети, отсутствие теоретических ограничений на количество узлов;
– Поддержка
разнотипных физических сред передачи данных, от витой пары до оптоволокна и
радиоканала;
– Эффективная реализация
режима реального времени.