Раздел 1. Управление техническими системами через автоматические системы в машиностроении
Тема 1.1.Система автоматического контроля
Вопросы:
1. Система автоматического контроля: общие сведения
2. Необходимость контроля положений и режимов в технологических процессах.
3. Структура системы автоматического контроля многих точек, назначение отдельных частей структуры.
4. Автоматическая сигнализация, указание значений контролируемых параметров, регистрация значений, сортировка изделий.
5. Контактный и бесконтактный способ измерения температуры
Контрольные вопросы
Вопрос 1. Система автоматического контроля: общие сведения
В автоматизированном производстве возрастает роль контрольных операций, т.к. человек контролёр не успевает производить эти операции или таких контролеров требуется очень много. Целесообразно производить промежуточный контроль, чтобы избежать массового брака.
Существует несколько видов контроля, эти виды отличаются по характеру использования информации, размеров и формы обрабатываемых деталей.
1. По характеру использования информации, полученной при контроле, различают:
а. Пассивный контроль – производится по завершению обработки деталей и служит для отбраковки негодных деталей и для набора остаточных данных, необходимых для выявления причин брака.
б. Активный контроль – постоянно определяется фактический размер деталей непосредственно на станке, при этом деталь может измеряться даже в процессе обработки, либо с остановкой станка. Информация при активном контроле подается в систему управления станком, либо в специальные адаптивные устройства – с целью управления самим процессом обработки.
2.По характеру взаимодействия измеряемого средства и обрабатываемой детали.
а. Контактные методы – являются традиционными и они обладают недостатком: на точность методов будет влиять износ измерения наконечников;
б. Бесконтактные методы – развиваются сравнительно недавно – оптические методы, в том числе использование лазерных систем. Они позволяют измерять размер детали дистанционно, т.е. не загромождая рабочей зоны даже в процессе обработки.
3. По степени достоверности получаемых результатов:
а. Прямой метод контроля, когда о размере детали мы судим по отсчету, снимаемого с данного устройства.
б. Косвенный – о точности детали в конце обработки судят по положению инструмента
Вопрос 2. Необходимость контроля положений и режимов в технологических процессах
Весьма важно увязать систему автоматизированного контроля (САК) с основными элементами технологической системы, что позволяет ставить вопрос о разработке технологического процесса измерений, сопровождающего процесс изготовления деталей (рис. 3.35). Непосредственно на участке механической обработки осуществляют контроль трех видов: установки заготовки в приспособление; изделия непосредственно на станке; выходной контроль. Контроль установки детали в приспособление можно осуществлять на конвейере перед станком или на станке непосредственно перед обработкой.
В
первом случае можно использовать дат
чики положения, расположенные на конвейере, или специальные измерительные установки с роботами. Бесконтактные датчики положения регистрируют отклонение действительного положения измеряемой поверхности от запрограммированного или разность условной базы и измеряемой поверхности (датчики касания). Измерительные устройства, устанавливаемые на стойках у конвейеров, позволяют контролировать не только положение заготовки в приспособлении до обработки на станке, но и параметры детали после обработки при перемещении ее в приспособлении на другую позицию.
Вопрос 3. Структура системы автоматического контроля многих точек, назначение отдельных частей структуры
Система автоматического контроля (САК) предназначена для автоматического контроля различных физических величин (параметров), сведения о которых необходимы при управлении объектом. Всякая система состоит из элементов, узлов и устройств, выполняющих ту или иную функцию; следовательно, систему автоматического контроля можно представить схематически.
Датчик (Д) измеряет значение контролируемого параметра объекта (О) и преобразует его в сигнал, удобный для усиления и передачи.Наибольшее применение находят датчики, преодразующие неэлектрическую величину в электрическую.
Усилитель (У) – устройство, усиливающее слабый сигнал, поступающий от датчика, так, что он становится достаточным для воздействия на исполнительный элемент.
Исполнительный элемент (ИЭ) – устройство, посредством которого выполняются заключительные операции.
Сигнализирующее устройство (СУ) – это автоматическая сигнализация характерных или предельных значений параметров (лампочки, звонок, сирена).
Указывающий прибор (ПУ) – автоматическое указание значений контролируемых параметров, может быть стрелочным, цифровым.
Регестрирующее устройство (РУ) – автоматическая регестрация значений контролируемого параметра, это самописец.
Прибор сортирующий (ПУ) – автоматическая сортировка различных изделий в зависимости от заданных значений контролируемых параметров.
Контроль линейных размеров деталей.
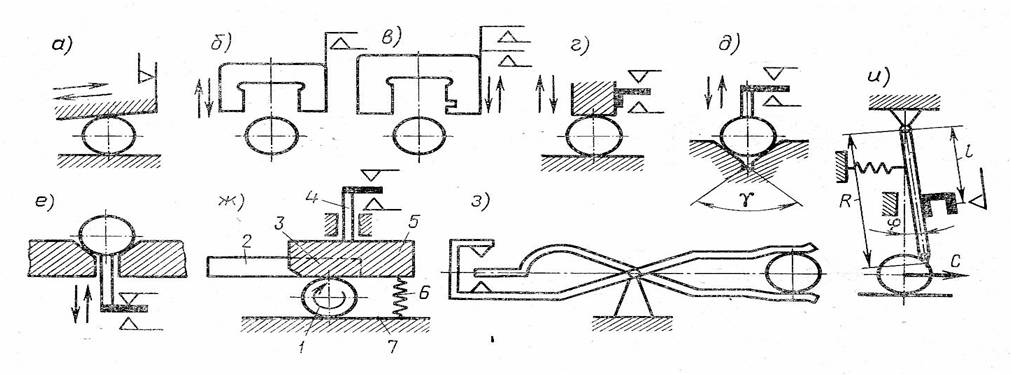
Расмотрим устройства для измерения наружных диаетров.Конусный калибр (а), однопридельная (б) или двухпредельная скоба (в) при своихперемещениях нажимают на соответствующие чувствительные элементы датчиков, чтобы подать команду на прибор, для сортировки или регулировки работы станка и на приборы для визуального наблюдения. Измерение размера детали от плоскости и при установки детали в призму характерно перемещением штока. Перемещение штока очень мало и точность измерительного устройства очень высокая.
Если надо измерить изделие в процессе перемещения, то можно применять схемы ж, з, и.В схеме ж изделие 1 прижимается к плоскому установочному элементу 7 толкателем 2 и губкой 5 с помощью пружины 6. Непараллельность сторон губки 5 до 0,4 мкм, что обеспечивает высокую точность показания прибора при перемещении штока 4. Толкатель 2 связан с губкой 5 шарниром 3. В схеме з размер диаметра измеряется губками-ножницами. В схеме и предельный размер детали определяют по величине отклонения штока.
Устройства предназначенные для измерения отвертий, могут работать по схемам:
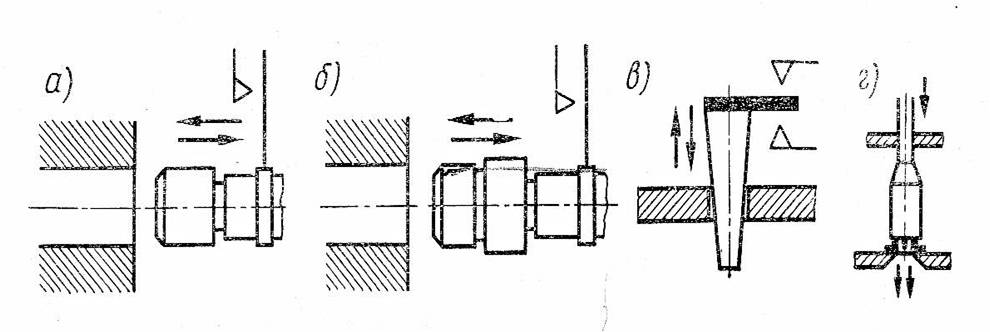
При контроле однопредельной и двухпредельной пробками (а и б) перемещение их в отверстие приводит к замыканию контактов для подачи сигналов на сортирующее устройство или в систему управления станком и прибор для визуального наблюдения . Аналогично измеряют конические пробки.
Очень удобно контролировать размер малых отверстий пневмодатчиками. Измерительное сопло подводится непосредственно к торцу отверстия так, чтобы контролируемое отверстие явилось продолжением отверстия сопла (г).Получившиеся изменение сечения отверстия сопла приводит к изменению давления в измерительной камере датчика. Датчик градуируется по эталонным отверстиям.
Автоматический контроль формы деталей.
Для контроля отклонений в поперечном сечении детали целендрической формы устанавливают деталь 1 контролируемой поверхностью в призму (а) и к проверяемой поверхности детали подводится шток амплитудного датчика. После этого деталь вращают в призме на 180 -200 градусов. Если колебания формы привысят допускаемую величину , то замкнутся один и затем другой контакты датчика.
При контроле отклонения формы поверхности (биения) относительно оси деталь 1 устанавливают в центрах 4 на измерительную базу, а к целендрической поверхности подводится оправка с 2 амплитудным датчикам или индекатором 3 (б).При повороте детали на 180-200 градусов измерительный шток или стрелка индекаторо будет отклонятся в одну и другую сторону, так как биение характерезуется изменением размера радиуса окружности в сечении, перпендикулярном оси детали.
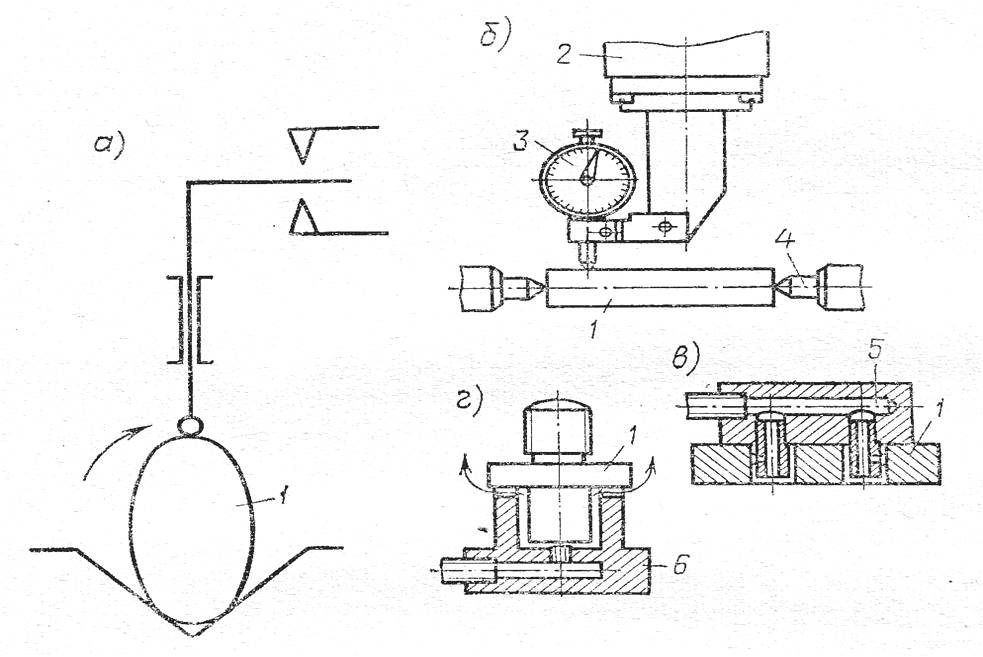
Для контроля отклонений от заданной формы могут быть использованы и пневматические датчики, контролирующие растояние между двумя отверстиями (в), размеры между торцем и буртиком (г) и др.
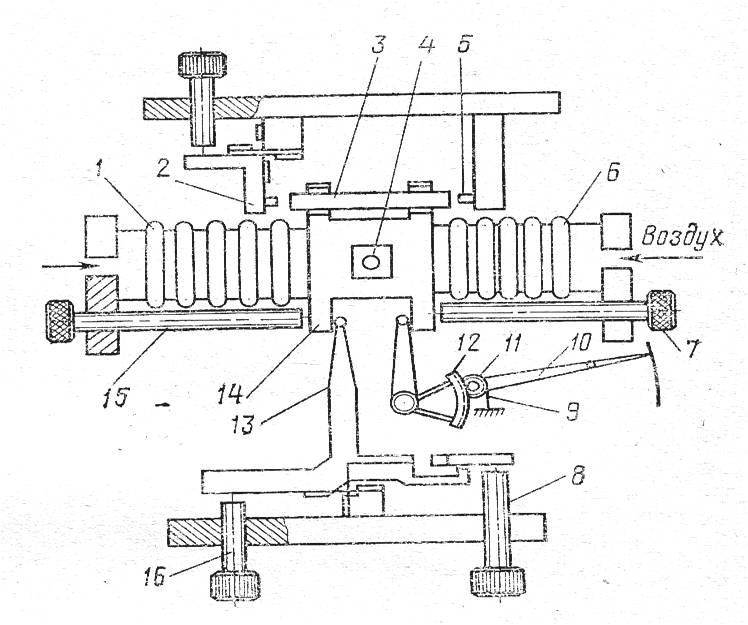
Для ускорения действия пневматических контрольных устройств используют промежуточнае звенья. На рис. Показана схема такого звена с двумя сильфонами. В сильфон 6 подаётся воздух постоянного давления, в сильфон 1 – воздух из рабочей камеры датчика. Давление воздуха в каждом сильфоне приводит его к сжатию или растяжению. В зависимости от разности давления в этих сильфонах перемещается связанная с ними каретка 14. При этом поворачивается рычаг 13 и замыкаются контакты 8 и 16, настраеваемые на предельные размры измеряемой поверхности детали.
Чтобы контролировать отклонения от геометрической формы, на каретку 14 устанавливают плавающий штифт 3, который замкнёт последовательно контакты 2 и 5, если отклонения привысят допуск. Упор 4 на каретки служит для ограничения перемещения самой каретки. Визуальное наблюдение размеров можно осуществлять по отсчётному устройству в виде рычага 12 с зубчатым сектаром, зацепляющимся с колесом 11, на оси которого стрелка 10. Мёртвый ход механизма выбирают с помощью волоска 9. По эталонам прибор настраивают винтами 7 и 15,регулирующими положение каретки 14.
Для автоматизированного контроля линейных размеров партии деталей разработана структурная схема контроля, которая включает модуль автоматизированной подачи изделия в зону контроля, измерительный модуль, а также систему синхронизации работы установки. Данная схема контроля реализована в макете лабораторной установки, представленной на рис. 1.....
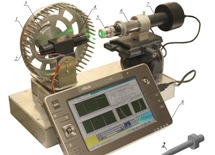
Рис. Автоматизированная система контроля линейных размеров партии деталей
Макет содержит управляемую шаговым двигателем револьверную головку 1, на которой закрепляется партия однотипных контролируемых деталей 2 (50 деталей). Детали подсвечиваются осветителем 4. Регистрация теневого изображения осуществляется микроскопом 6, который состоит из микро объектива 5, окулярной цифровой камеры 7. Сигнал с камеры поступает в компьютер 7. Виртуальные приборы на компьютере 8 управляют поворотом револьверной головки, обработкой видеосигнала и измерением линейных размеров деталей.
В качестве образцов использовалась партия цилиндрических изделий (рис. 1, поз. 2) 3.35 мм, а также нарезка из низкокачественной необработанной проволоки диаметром 1 – 2 мм. Калибровка измерительной схемы проводилась в программе Webbers ScopePhoto по объект микрометру 1 мм – 0.01 мм (ГОСТ 7513-55).
Измерения на микроскопе OptiTech с объективом OptiTec 4X со стандартной длиной тубуса (190 мм) показали, что в первом случае диаметр был равен 523±2 пкс, во втором – 1233.29±2 пкс. Таким образом, в первом случае измеряемый размер равен 1.210 мм, а во втором – 1.203 мм. Динамический диапазон измерения и абсолютная погрешность для первого сенсора будет составлять 2.9±0.005 мм, для второго – 3.1±0.003 мм соответственно.
Вопрос 4. Автоматическая сигнализация, указание значений контролируемых параметров,
регистрация значений, сортировка изделий
Автоматическая сигнализирующая система используется для оповещения обслуживающего персонала о возникших отклонениях в контролируемом объекте путем подачи звуковых или световых сигналов. Системы автоматической сигнализации в зависимости от их назначения подразделяются на контрольные и предупредительные.
Предупредительная сигнализация извещает обслуживающий персонал о различных режимах работы оборудования или о непредвиденном его выключении, вызванном неисправностью или внешними причинами. Получаемая обслуживающим персоналом информация может быть как звуковой, так и световой.
Для подачи звуковых сигналов используются сирены, звонки, гудки, зуммеры и магнитофоны с предварительно записанными сообщениями. Громкость и частота звукового сигнала должны обеспечивать его хорошую слышимость на фоне производственных шумов (уровень сигнала должен быть выше на 10 дБ общего шума). Повышенной надежностью обладают модулированные (по высоте) и прерывающиеся во времени звуки.
В качестве визуальных сигнализаторов используются световые приборы: фонари, прожекторы, табло, транспаранты с надписью, указывающие характер событий, электромеханические реле с сигнальными флажками.
Отдельные сигнализаторы могут объединяться в комплекс (на пультах управления), дающий изображение текущего состояния контролируемого объекта.
Конструкция и параметры светосигнальных устройств должны обеспечивать надежное фиксирование сигнала глазом человека. Для этого необходимо создавать такую освещенность, при которой начинает восприниматься цвет сигнала. Сигнальные цвета должны быть контрастными по отношению друг к другу и окружающему фону. В аварийной световой сигнализации предпочтение отдается красному цвету, который лучше всего виден, сквозь пыль и дым. Хорошо воспринимается мигающий свет с частотой мигания не более 10 Гц и продолжительностью не менее 0,05 с.
Для надежного обнаружения светового сигнала сигнализаторы должны располагаться в пределах 30° от нормальной оси зрения оператора. В качестве источников света в сигнализаторах используют лампы накаливания, лампы тлеющего разряда и электролюминесцентные приборы.
Вопрос 5. Контактный и бесконтактный способ измерения температуры
Пирометр - измерительный прибор для бесконтактного измерения температуры, принцип работы прибора основан на использовании инфракрасного излучения.
Принцип действия инфракрасного пирометра основан на измерении абсолютного значения излучаемой энергии одной волны в инфракрасном спектре. На сегодня это относительно недорогой бесконтактный метод измерения температуры. Данные устройства могут наводиться на объект с любой дистанции и ограничены лишь диаметром измеряемого пятна и прозрачностью окружающей среды. Они идеальны для переносных моделей, и поэтому могут работать по принципу "навел и выстрелил".
Инфракрасные термометры, часто называемые пирометрами, используют принцип детектора инфракрасного излучения. Интенсивность и спектр излучения зависит от температуры тела. Измеряя характеристики излучения тела, пирометр косвенно определяет температуру его поверхности.Назначение пирометров
- измерение температуры удаленных и труднодоступных объектов;
- измерение температуры движущихся частей;
- обследование частей, находящихся под напряжением;
- контроль высокотемпературных процессов;
- регистрация быстро изменяющихся температур;
- измерение температуры тонкого поверхностного слоя;
- обследование частей, не допускающих прикосновения;
- обследование материалов с низкой теплопроводностью или теплоемкостью;
- экспресс - измерения.
Области применения пирометров
- теплоэнергетика: котлы, турбины, бойлеры, теплотрассы, паропроводы;
- электроэнергетика: трансформаторы, кабели, контакты, шины под напряжением;
- металлургия и металлообработка: печи, станы, прессы;
- электроника: контроль температуры элементов и деталей;
- диагностика двигателей внутреннего сгорания;
- электродвигатели и подшипники;
- контроль температуры производственных процессов;
- контроль условий хранения и перевозки пищевых продуктов;
- обследование зданий и сооружений;
- системы отопления, вентиляции и кондиционирования;
- обследование холодильной техники;
- оснащение пожарных бригад.