Тема 4.3. Системы программного управления промышленным оборудованием
Вопросы:
1. Системы программного управления промышленным оборудованием как средство решения задач управления.
2. Числовое программное управление, структура систем ЧПУ, использование микроЭВМ со специализированным программным обеспечением для решения задач управления.
3. МикроЭВМ и контроллеры периферии.
Вопрос 1. Системы программного управления промышленным оборудованием как средство решения задач управления.
Системы программного управления промышленным оборудованием
Программная система управления
В настоящее время в промышленности все больше находят применение станки с программным управлением. В этих стан¬ках переход от обработки одной детали к другой осуществля¬ется сменой программ, записанных на перфоленте, перфокарте, магнитной ленте. Под программой понимается полное и точ¬ное описание технологического процесса обработки изделия в режиме автоматической работы станка. Таким образом носите¬лем информации в этом случае является программа, которая связана со станком, что способствует быстрой смене техноло¬гического процесса.
Достоинство станков с цифровым программным управлением (ЦПУ) или с числовым программным управлением (ЧПУ) со¬стоит в следующем: освобождение человека от работы на стан¬ке; увеличение производительности труда; обеспечение более плотной загрузки оборудования; эффективность оборудования: один станок с программным управлением заменяет до восьми обычных станков; из станков с ЧПУ легко скомпоновать авто¬матические линии; введение программного управления позво¬ляет централизовать подготовку технологических программ для отрасли промышленности с обеспечением квалифицированными кадрами программистов; повышается качество обработки и уменьшается процент брака.
Автоматические линии из станков с ЧПУ легко подключа¬ются к электронно-вычислительным машинам. ЭВМ по заранее составленной программе организует работу всей линии, а в слу¬чае переналадки вводят код нового изделия и ЭВМ перестраи¬вает оборудование. Особенно эффективно применение про¬граммной системы управления при обработке деталей сложной формы.
В то же время при применении станков с ЧПУ необходимо учитывать, что требуется подготовка программистов, усложня¬ется ремонт оборудования и нужно проводить типизацию изде¬лий для обработки.
Различают два способа программирования. Первый способ заключается в том, что берется чертеж детали, который коди¬руется в виде таблицы или аналитического уравнения. При этом вся траектория движения инструмента и рабочих органов станка разбивается и а элементарные участки. Координаты каждого участка в виде приращений по осям х? у, z наносятся, на-пример, на магнитную ленту в виде импульсов напряжений или модулированного сигнала, а на перфоленту и перфокарту в виде отверстий. На магнитной ленте имеются для записи не¬сколько дорожек (шесть, восемь) для того, чтобы программо¬носитель был меньше по объему. Программа вводится в уни-версальную или специализированную вычислительную машину. Если программа большая, то вычислительное устройство встраи¬вается в систему управления станком, в случае простой про¬граммы к одной УВМ или ЭУВМ подключено несколько станков с программным управлением.
Второй способ составления программы заключается в «обу¬чении» управляющей машины. Здесь нет необходимости состав¬лять по чертежу таблицу или уравнение траектории движения инструмента или детали. В этом случае на станок устанавли¬вается заготовка и подключается программное устройство. Ра-бочий изготавливает по чертежу первую деталь с управлением вручную и данные обработки автоматически записываются на магнитную ленту от станка. При «обучающем» способе можно использовать копир или обводку контура чертежа. Эта анало¬говая система управления, но применима она только для изго¬товления деталей, не требующих высокой точности.
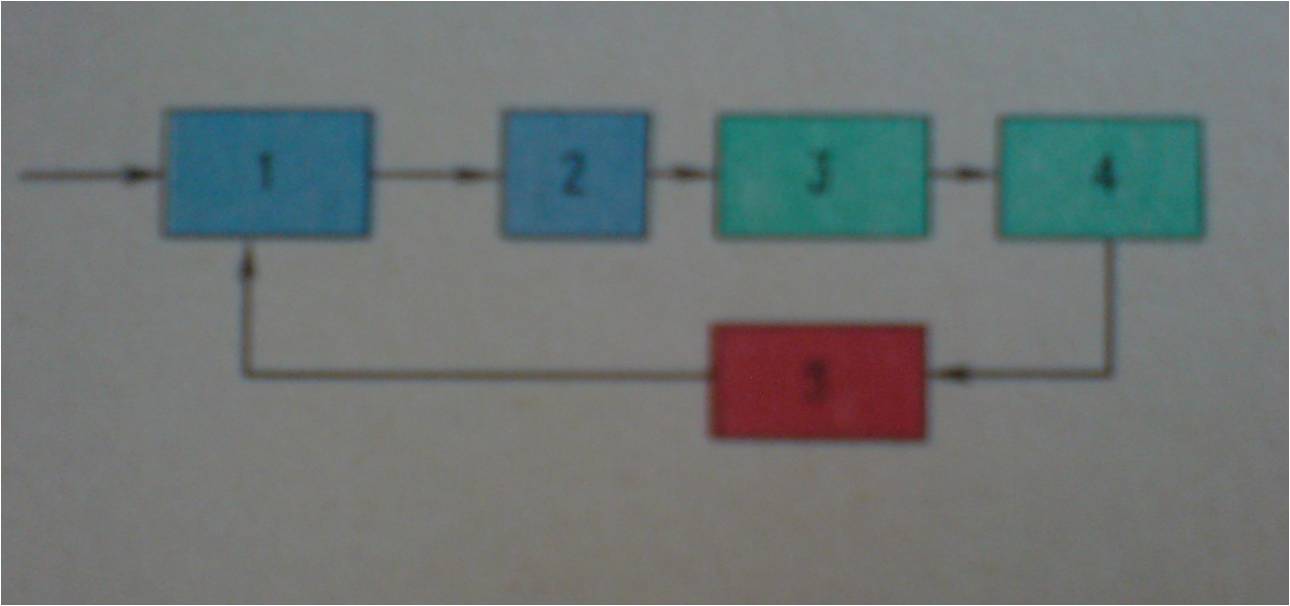
Упрощенная структурная схема программного управления с обратной связью
Последовательность работы про¬граммного управления следующая. Записанную на перфора¬торе ленту с программой вводят в считывающее устройство 1. Лента перемещается, а датчик воспринимает программу и вы¬дает се в преобразователь 2 в виде импульсов напряжения. В преобразователе 2 происходит запоминание, распределение (сортировка) и усиление поступивших управляющих сигналов. Из преобразователя сигналы подаются в исполнительный ме¬ханизм 3, который приводит в действие рабочие органы 4 ав¬томата. Узел обратной связи 5 обеспечивает сравнение дейст¬вительных перемещений рабочих органов с программными. Для этой цели используется измерительное устройство. В случае отклонения от программы срабатывает корректирующее устройство узла обратной связи, которое посылает поправочные им¬пульсы в считывающее устройство 1 или в преобразователь 2.
Программоносители для записи работы автомата изготовля¬ют из различных материалов. Наибольшее распространение по¬лучили бумажная перфорированная лента и магнитная лента. На магнитной ленте запись выполняется в виде поперечных магнитных штрихов. Лента движется непрерывно и использу¬ется для записи сложных процессов и их быстрого воспроизве¬дения.
Программоносители
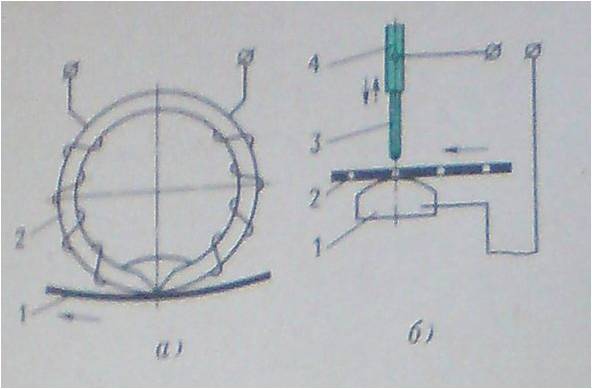
Считывание программы с магнитной ленты производится следующим образом рис а). Лента 1 с магнитной записью протягивается мимо магнитной головки 2, в которой возбуж¬дается электродвижущая сила. Полученные сигналы через уси¬литель подаются к исполнительным механизмам. Скорость про¬тяжки ленты мимо магнитной головки равна скорости, при ко¬торой производилась запись.
На перфорированной бумажной ленте программа фиксиру¬ется в виде отверстий, расположенных в определенном порядке на нескольких дорожках. Считывание производится (рис б). токопроводящим штифтом 3 ползуна 4, который перемещается вертикально над планкой 1 с движущейся по ней лентой 2. При прохождении отверстия под штифтом последний замыкает цепь с планкой и выдает соответствующие команды.
Программа может быть записана в виде кода. В этом слу¬чае она задается рядом зашифрованных цифровых значений координат точек обрабатываемой поверхности. Программа по¬ступает в дешифратор, прочитывается и сигналы подаются в вы¬числительное устройство для выработки управляющих сигналов. Кодирование применяется для записи сложных программ. При некодированной записи сигналы со считывающего устройства подаются непосредственно к исполнительным органам.
Считывание программы с перфорированной бумажной ленты
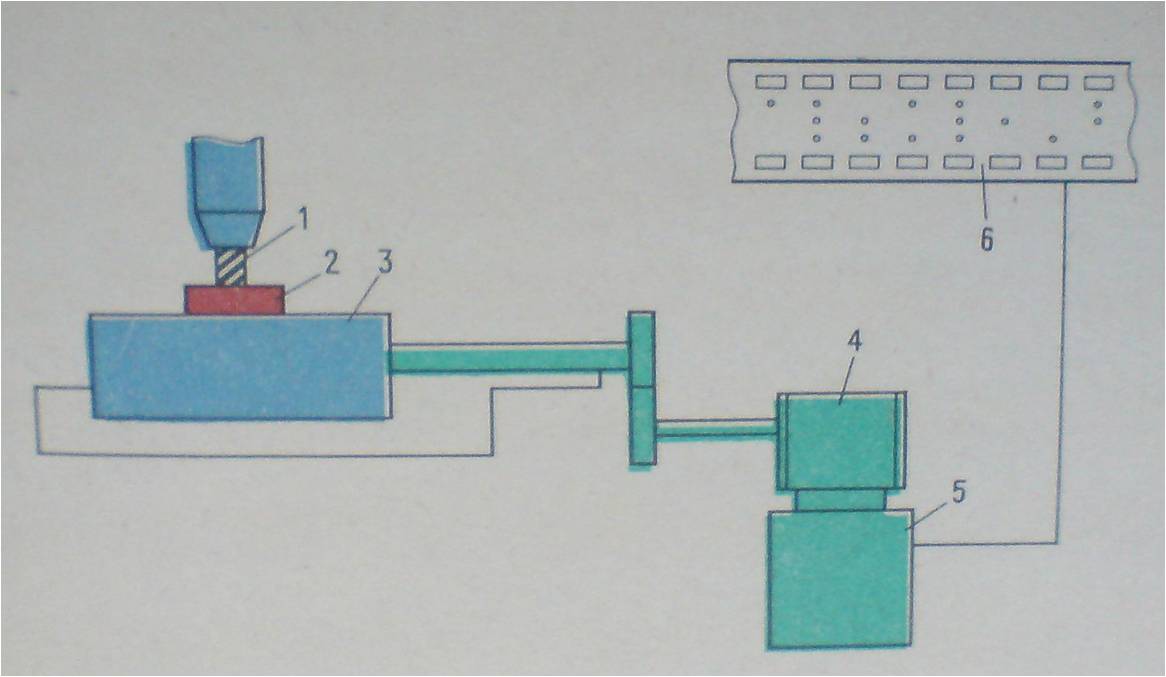
Фрезерный станок оснащен
шаговой системой цифрового управления. Программа считыва
ется с бумажной перфорированной ленты 6 и вводится в блок управления 5 который подключает обмотки электромеханического устройства шагового двигателя 4. Шаговый двигатель приводит в движение предметный стол 3 станка и деталь 2 обрабатывается режущтм инструментом 1
Схема работы разомкнутой системы
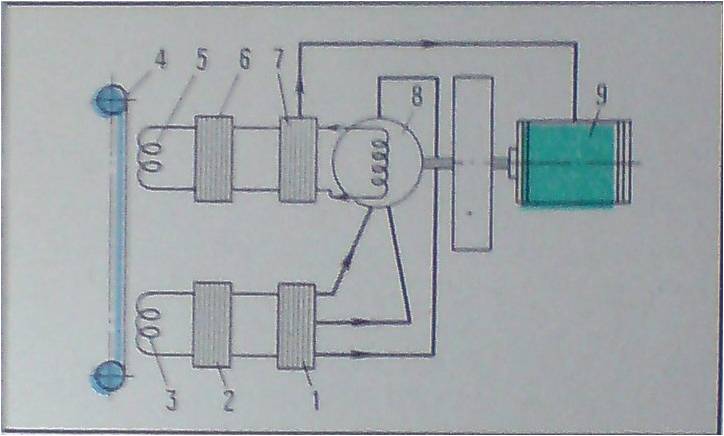
Программа считывается с магнитной ленты 4 магнитной головки 3 после усилителя 2 и преобразователя 1 подается на обмотку статора сельсина 8. В то же время сигнал управле¬ния, считанный головкой 5 через усилитель 6, подается на вход фазового индикатора 7, в который также поступает сигнал об¬ратной связи с сельсина 8 на другой вход. Полученный сигнал рассогласования, который пропорционален разности фаз напря¬жений, подается на управление двигателем 9 привода станка.
Система программного управления по трем координатам обеспечивает получение заданных размеров и конфигурации об¬рабатываемого изделия, выбор частоты вращения шпинделя, ве¬личины подачи суппорта, включение ускоренных перемещений, смену инструмента, включение системы охлаждения и уборки стружки. Программа записывается на стандартной магнитной восьмидорожечной ленте в коде. Имеется возможность ручного ввода коррекций. Для ручного набора координат на пульте уп¬равления задаются величины перемещения суппорта, подач, ча¬стоты вращения шпинделя.
Системы числового программного управления станками
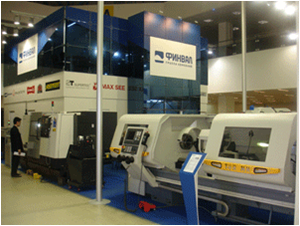
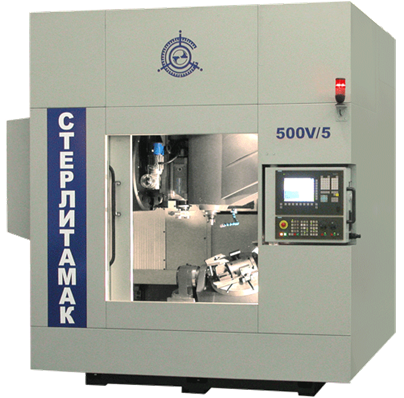
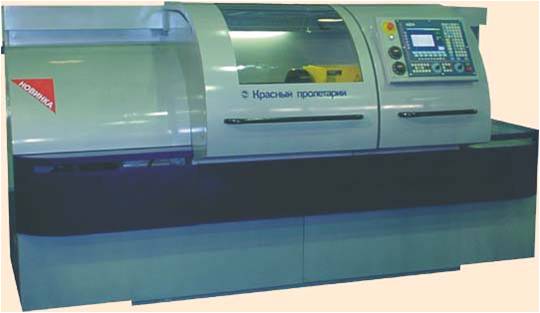
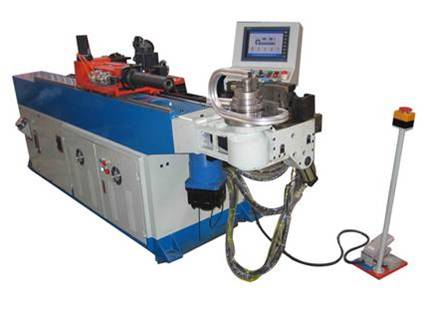
Числовое программное управление станком - управление обработкой заготовки на станке по управляющей программе, в которой данные заданы в цифровой форме. Совокупность функционально взаимосвязанных и взаимодействующих технических и программных средств, обеспечивающих числовое программное управление станком, называют системой числового программного управления.
Числовое программное управление станками по технологическим признакам подразделяют на позиционное, контурное, адаптивное и групповое.
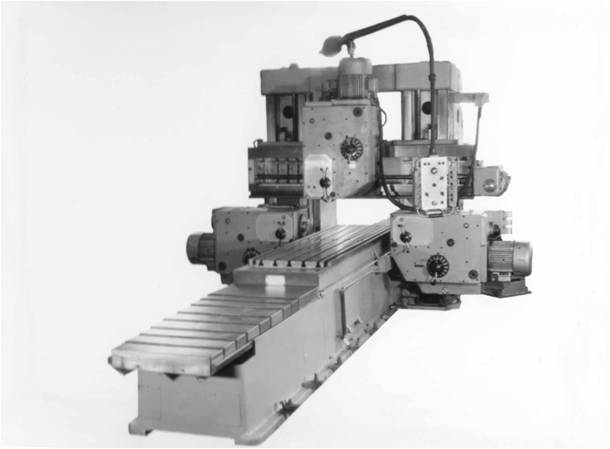
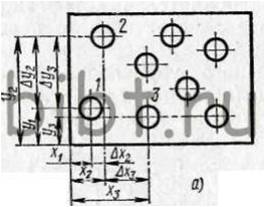
Позиционное управление
Позиционное управление - числовое программное управление станком, при котором перемещение его рабочих органов происходит в заданные точки, причем траектории перемещения не задаются. Такое управление применяют в основном в сверлильных и расточных станках для обработки плоских и корпусных деталей с большим числом отверстий.
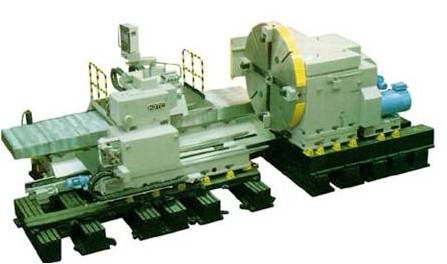
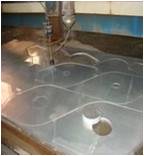
Контурное управление
Контурное управление - числовое программное управление станком, при котором перемещение его рабочих органов происходит по заданной траектории и с заданной скоростью для получения необходимого контура обработки. ЧПУ для контурной обработки позволяет осуществлять непрерывное управление скоростями рабочих движений инструмента относительно заготовки и обеспечивает их заданные положения в каждый момент времени в соответствии с профилем детали, т. е. обеспечивает автоматический обход режущего инструмента по заданному контуру детали. Для обработки плоских деталей используют системы контурной двухкоординатной, а для объемных деталей - трехкоординатной обработки.
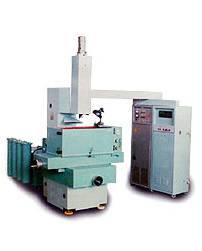
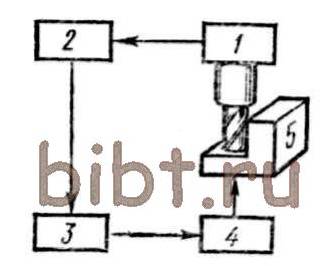
Адаптивное управление
Адаптивное управление - числовое программное управление, при котором обеспечивается автоматическое приспособление процесса обработки заготовки к изменяющимся условиям обработки по определенным критериям.( Адаптивное управление обеспечивает наилучшее использование возможностей станка при обработке заготовки с изменяющимися параметрами, при этом значительно упрощается подготовка управляющих программ)
Упрощённая блок-схема адаптивного управления
Самоприспосабливающиеся системы В простейшем виде адаптивного управления происходит автоматическое регулирование по небольшому числу параметров. информацией от считывающего устройства. Тем самым корректируется процесс обработки при отклонении измеряемого параметра от заранее установленных границ
При фрезеровании заготовки 5 происходят упругие отжатая инструмента, что снижает точность обработки. Для измерения величины отжатия шпинделя на его нижнем конце размещены два датчика 1, которые измеряют отжатие шпинделя (а вместе с ним и режущего инструмента) по осям X и Y. Сигналы от датчиков после соответствующего их усиления подаются в логическое устройство 2 и в блок управления 3 станком. Этот блок через сервомеханизм 4 автоматически изменяет команды, закодированные ранее на перфоленте, тем самым оптимизируя режимы резания.
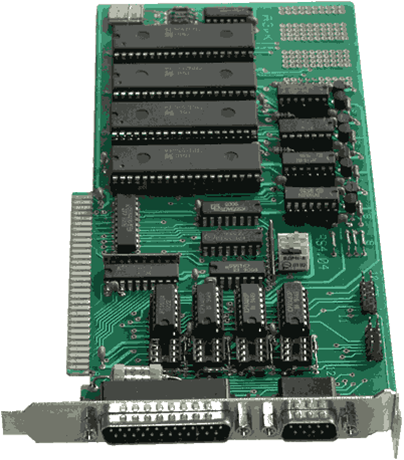
Групповое управление
Групповое управление - числовое программное управление группой станков от ЭВМ, имеющей общую память для хранения управляющих программ, распределяемых по запросам от станков.
Одним из основных элементов контурных ЧПУ является интерполятор - вычислительное устройство для определения координат точки, непрерывно движущейся по кривой о заданными параметрами..
В современных контурных системах ЧПУ команды на перемещение рабочих органов выдаются дискретно, в виде единичных кратковременных управляющих воздействий (управляющих импульсов). Интерполятор обеспечивает такое распределение во времени поступающих импульсов между приводами подач, при котором инструмент перемещается с максимальным приближением к заданной прямой (при линейной интерполяции) или к дуге окружности (при круговой интерполяции) с определенными шагами.
Системы автоматического управления (САУ) делят на разомкнутые, замкнутые и комбинированные.
Разомкнутые системы характеризуются наличием только одного потока информации, направленного от устройства, считывающего программы, к исполнительному устройству. При вводе программоносителя в считывающее устройство на выходе его появляются командные сигналы. После необходимых преобразований электронный блок управляет шаговым двигателем и исполнительным устройством, которое перемещает рабочий орган станка в заданное положение. Соответствие действительного перемещения заданному при этом не контролируется. Звенья разомкнутой системы не охвачены обратной связью.
Замкнутые системы имеют два потока информации: один - от считывающего устройства, другой - от датчика действительного перемещения или положения рабочего органа.
При считывании программы на выходе считывающего устройства появляются командные сигналы. После необходимых преобразований блок согласования направляет соответствующий сигнал в сравнивающее устройство замкнутой системы.
Вопрос 2. Числовое программное управление, структура систем ЧПУ, использование микроЭВМ со специализированным программным обеспечением для решения задач управления.
Одним из основных направлений повышения эффективности общественного производства является автоматизация технологических процессов на основе широкого использования автоматизированного высокопроизводительного оборудования и машин. Автоматизация оборудования не только способствует повышению производительности и качества продукта, но также частично или полностью освобождает человека от непроизводительного и утомительного труда, оставляя за ним функции контроля за этим оборудованием и поддержания его работоспособности.
Применение станков с числовым программным управлением – одно из наиболее прогрессивных направлений автоматизации металлообработки на промышленных предприятиях. На станках с ЧПУ происходит автоматическое управление обработкой на станке или перемещение рабочих органов по заданной программе .
Станки с ЧПУ имеют целый ряд преимуществ по сравнению с аналогичными станками с ручным управлением:
1) повышается производительность;
2) сочетается гибкость универсального оборудования с точностью и производительностью станка-автомата, что и позволяет решать вопрос комплексной автоматизация производства;
3) качественно перевооружается машиностроение на базе современной электроники и вычислительной техники;
4) снижается потребность в квалифицированных рабочих-станочниках, а подготовка производства переносится в сферу инженерного труда;
5) сокращается время пригоночных работ в процессе сборки, так как детали, изготовленные по одной программе, являются взаимозаменяемыми;
6) сокращаются сроки подготовки и перехода на изготовление новых деталей благодаря централизованной записи программ и более простой и универсальной технологической оснастке;
7) снижается продолжительность цикла изготовления деталей и уменьшается запас незавершенного производства.
1. КЛАССИФИКАЦИЯ СТАНКОВ
С ЧИСЛОВЫМ ПРОГРАММНЫМ УПРАВЛЕНИЕМ
Шифрование программы работы какой-либо машины в форме пробивок на перфокартах, перфолентах или на других носителях программы применяют давно. Этот принцип применялся в ткацком станке Жаккара, созданном в 1801 г., в «механическом пианисте» — пианоле, в наборной машине — монотипе и т. д. Все эти машины работали по принципу: есть отверстие — действие совершается, нет отверстия - действие не совершается. Причем действия были предельно просты и не зависели от сложности программы. В станкостроении программное управление стало применяться значительно позже из-за сложности процессов металлообработки. Решение этой задачи стало возможным, когда машиностроение, электроника, вычислительная техника достигли определенного уровня развития.
При автоматическом управлении станком необходимая последовательность команд задается программоносителем. Программоноситель может быть изготовлен в виде материального аналога обрабатываемой детали (кулачков, копиров, упоров и т. д.). Например, в автоматах и полуавтоматах кулачки распределительного вала задают последовательность и величину перемещений рабочих органов. Профиль кулачков соответствует запрограммированной обработке. В токарных и фрезерных копировальных станках форма обрабатываемой детали зависит от формы шаблона или копира. При смене объекта производства необходимо подготовить новые кулачки, копиры и т. д. Производительность станков высокая, но время переналадки достаточно велико.
Наибольшей гибкостью и быстротой переналадки обладают станки с программным управлением (ПУ). Программа управления станком — это последовательность команд, обеспечивающая заданное функционирование рабочих органов станка. При ручном управлении станком необходимую последовательность команд задает рабочий, который, предварительно изучив чертеж и техническую документацию, составляет программу работ, обрабатывает деталь, измеряет ее, производит сравнение с чертежом и при наличии рассогласования устраняет неточности.
Программа может быть записана на программоносителях в виде перфоленты, перфокарты, гибких магнитных дисков, магнитной ленты. Программу можно вводить и вручную с помощью клавишных панелей. Такие программоносители позволяют автоматизировать процесс подготовки программ и снизить трудоемкость изготовления программоносителей.
Программоноситель может содержать как геометрическую, так же технологическую информацию. Технологическая информация обеспечивает определенный цикл работы станка: последовательность ввода в работу различных инструментов, изменение режимов резания, включение или отключение подачи смазочно-охлаждающей жидкости, зажим или разжим исполнительных органов станка и т. д. Геометрическая информация характеризует форму, размеры элементов обрабатываемой заготовки и инструмента и их взаимное положение в пространстве.
По виду управления станки с ПУ делят на станки с системами циклового программного управления (ЦПУ) и станки с системами числового программного управления (ЧПУ). Системы ЦПУ более просты, так как в них программируется только цикл работы станка, а величины рабочих перемещений, т. е. геометрическая информация, задаются упрощенно, например, с помощью упоров. В станках с ЧПУ управление осуществляется от программоносителя, на который в числовом виде занесена и геометрическая, и технологическая информация.
В отдельную группу выделены станки с цифровой индикацией и преднабором координат. В этих станках имеется электронное устройство, которому задаются координаты нужных точек (преднабор координат), и крестовый стол, снабженный датчиками положения, выводится в требуемую позицию. При этом на экране высвечивается каждое мгновенное положение стола (цифровая индикация). В таких станках (чаще всего расточных) может применяться или преднабор координат или цифровая индикация; исходная программа работы задается станочником.
Первое поколение станков с ПУ в нашей стране было создано на базе серийно выпускаемых универсальных станков, промышленный выпуск их начался в 1959 г. От базовых моделей станки с ЧПУ отличались только автоматизацией привода подач: устанавливались шаговые электрогидравлические или гидравлические приводы, беззазорные редукторы, винт-гайки качения. Устройство ЧПУ, выполненное на электронных лампах, давало возможность получать необходимые размеры обрабатываемой заготовки при регулируемой подаче.
Для станков с ЧПУ второго поколения характерно применение систем управления, выполненных на полупроводниковых приборах. Такие системы могли изменять в автоматическом цикле не только подачи, но и частоту вращения шпинделя, давать технологические команды на автоматическую смену инструмента, подачу СОЖ, зажим детали и т. д. Высокая стоимость этих систем сделала нерентабельным применение их на универсальных станках с малой степенью автоматизации. Поэтому были созданы модели станков, имеющие устройства автоматической смены инструмента, автоматические коробки скоростей (АКС) и т. д. Одновременно широко велась разработка методов автоматического программирования и необходимого математического обеспечения. В этот же период выяснилось, что моральное старение устройств ЧПУ наступает в 2 — 2,5 раза быстрее, чем станков. Поэтому этапы развития ЧПУ достаточно условны, и каждый последующий этап развития содержит некоторые элементы предыдущего этапа и развивается параллельно.
Третий этап развития станков с ЧПУ характеризуется качественным изменением системы ЧПУ. Для управления станками используют малые ЭВМ (мини-ЭВМ). Это дает возможность выпускать станки с очень высоким уровнем автоматизации, усложненной конструкции с широкими технологическими возможностями — многоцелевые станки. Станки с ЧПУ компонуют в автоматизированные' участки с управлением от ЭВМ. При широком использовании промышленных роботов на этих участках становится возможной «безлюдная» технология.
2. ОСНОВНЫЕ СВЕДЕНИЯ О ЧИСЛОВОМ ПРОГРАММНОМ УПРАВЛЕНИИ
Числовое программное управление (ЧПУ) обеспечивает управление движениями рабочих органов станка и скоростью их перемещения при формообразовании, а также последовательностью цикла обработки, режимами резания, различными вспомогательными функциями.
Станки с ЧПУ обслуживаются различными заводскими службами. Рассмотрим составные элементы комплекса ЧПУ (рис. 1)
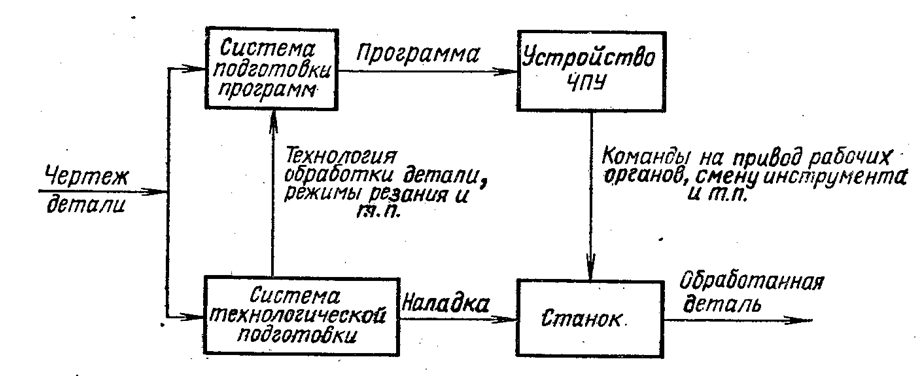
Рис.1 Комплекс числового программного управления
Чертеж детали одновременно поступает в систему подготовки программы и систему технологической подготовки, обеспечивающей отдел подготовки программ данными о технологическом процессе обработки детали, режимах резания и т. д. На основании полученных данных создается управляющая программа. Программа поступает в устройство ЧПУ, которое перерабатывает полученную информацию и подает команды рабочим органам станка. Наладчики устанавливают на станок инструменты и приспособления согласно документации, разработанной в системе технологической подготовки. Данный комплекс ЧПУ может видоизменяться в зависимости от вида программоносителя, способа кодирования информации и метода ее передачи в систему ЧПУ. В качестве программоносителя используют перфоленты, гибкие магнитные диски или кассеты, реже — магнитные ленты. При подготовке программы производится кодирование исходной информации и представление ее в виде символов. Для кодирования используют различные коды (двоично-десятичные, двоичные и т. д.). Система подготовки программ может быть автоматизированной и ручной, ручная подготовка применяется значительно реже. Программу можно вводить и с помощью клавиш непосредственно на станке, как это делается в оперативных системах ЧПУ типа «Электроника НЦ-31». В качестве встроенного в систему ЧПУ накопителя программ используют магнитные ленты или гибкие магнитные диски.
Перфолента — наиболее распространенный программоноситель, этому способствуют ее достоинства: дешевизна и простота хранения, малый объем перфоленты, так как ее длина зависит не от времени обработки детали на станке, а от сложности детали, числа опорных точек и т.д. Программа записанная на перфоленте, может содержать неограниченное число технологических команд. Устройство управления от перфоленты позволяет вводить коррекции на длину инструмента, его положение и т. д.
Пробитое отверстие на перфоленте соответствует наличию сигнала, при отсутствии отверстия — сигнала не будет. Геометрическая информация на перфоленте заносится в виде координат опорных точек. Опорные точки 1, 2, 3 (рис. 2) расположены на стыке элементарных участков обрабатываемой заготовки. Криволинейные участки (точки 2—6, 7—11) в зависимости от способа аппроксимации и требуемой точности можно разбить на ряд элементарных участков.
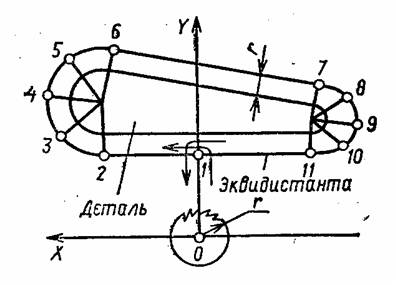
Рис.2 Контур детали с опорными точками
Перемещение рабочих органов между опорными точками определяется автоматически от интерполяторов. Центр фрезы перемешается по эквидистанте, отстоящей от контура детали на величину радиуса фрезы. Интерполятор декодирует геометрическую информацию перфоленты, т. е. преобразовывает ее в определенную последовательность распределенных во времени и по координатным осям импульсов, каждый из которых подразумевает элементарное перемещение рабочих органов станка.
Информация на перфоленту наносится перфораторами. Считывание информации может осуществляться различными способами (рис. 3) . При электрическом способе считывания (рис. 3, а) контактные щетки 2 при наличии отверстия в перфоленте Пл вступают в контакт с барабаном 1 и выдают сигнал в схему автоматики. Метод обеспечивает достаточно высокое быстродействие, но имеет низкую надежность из-за возможности загрязнения щеток.
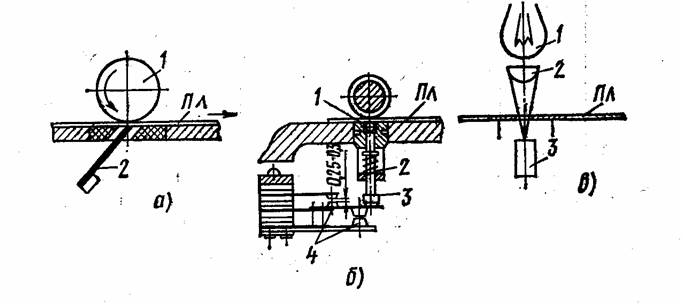
Рис.3. Схемы способов считывания перфорированного программоносителя
В электромеханических системах считывания (рис. 3, б) перфолента Пл ощупывается шариками 1, поджимаемыми к ней пружинами 2 через шрифты 3. При наличии пробивки замыкаются соответствующие контакты 4, передается команда в схему автоматики станка и выдается сигнал большой величины. Способ имеет низкую надежность и малое быстродействие. Наиболее распространены фотоэлектрические системы считывания (рис.3, в). При наличии пробивки от лампы 1 через линзу 2 срабатывает фотоэлемент 3 и выдает команду в систему автоматики. Такие системы имеют высокое быстродействие (до 1000 знаков) и высокую надежность. Недостатки способа: малый сигнал и малая помехозащищенность.
При централизованном управлении группой станков с ЧПУ от ЭВМ запись программы на перфоленту или магнитную ленту не нужна. Программа обработки в виде электрических сигналов передается к устройствам ЧПУ, находящимся у станков. Эти устройства имеют в свою очередь канал связи с ЭВМ, по которому из памяти ЭВМ выбирается нужная программа, и в нее вводятся различные коррекции.
Вопрос 3. МикроЭВМ и контроллеры периферии.